Process
The Production Process of High Quality
Stainless Steel Tube
Teshima's Stainless steel tubes are manufactured through many steps to ensure the best quality standard.
We support more than 7,000 types of standards and ship about 400 types per month. To increase production efficiency, we have introduced an IT process control system and are implementing traceability-based production control in each process.
In each process, we thoroughly control the process to improve the accuracy of dimensional standards, and in order to maintain quality, we set strict quality item standards in each process and carry out strict quality checks, and products with quality accuracy.
Standard Process
1. Welding Process
Tube welding and forming depends on the grade and application specifications. At Teshima Corporation, we use TIG welding, a process ideal for small diameter tube fabrication. Steel sheets enter a welding machine where they are coiled and welded. When the steel sheets enter the machine, they are formed to a coil. These coils are then welded at the seam to form a tube.
The standard materials used are:
- 304 stainless steel
- 304L stainless steel
- 316 stainless steel
- 316L stainless steel
2. Drawing/ Floating Process
Floating/Drawing process of pulling a metal bar, rod, or wire through the whole of a die to alter its finish, shape, size, and/or mechanical properties. The tube drawing technique reduces the outer diameter, inner diameter, and wall thickness of the tube. The integrity of the surface of the tube is maintained, ideal for stainless steel tubes.
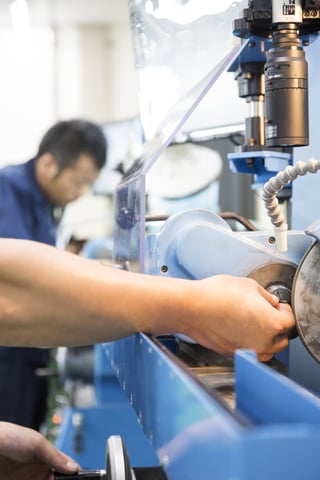
3. Annealing
Annealing is the process of heating metal above re-crystallization and cooling it back to room temperature. When metal is formed to shape, the molecular bonds tighten making the metal stiff. To restore ductility, the metal is process through annealing machines. At Teshima Corporation, we specialize in annealing of stainless steel. With ten annealing machines in our factory, orders are processed quickly and efficiently.
4. Sinking Process
Tube sinking is a drawing process that shrinks tubes to a small diameter. In this drawing method, a tube is process through a die without a mandrel being inserted. With a mandrel, good inner surface quality is not guaranteed. The outer surface integrity is determined by the die angel. The die used gives a standard surface. A tube can be shunk down to a significant value of its original size. Tube sinking is perfect for jobs where cost is critical.
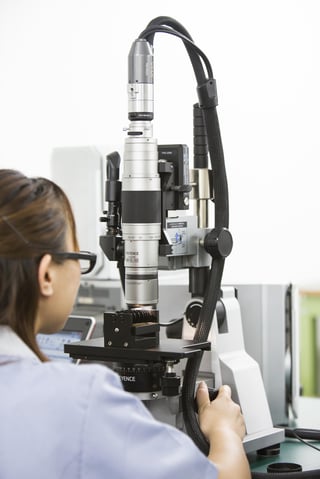
5. Inspection and Testing
We perform inspection checks to validate the integrity of our products before shipping out to our customers.
Common testing includes:
- OD/ID/WT Tolerance
- Welding condition
- Cracks
- Scratches
- Bending
- Discoloration
- Hardness and other inspections
Certification
Teshima has the latest technology in machinery & production lines for Hypodermic Stainless Steel Tubing. Human efficiency and Technology complement each other toward excellence. Our strict quality assurance process meets the highest environmental standards that has made us acquire ISO 9001:2015 and ISO 14001:2015